Zusammenspiel zwischen DLC-Schichten und ZDDP-Schmierstoff: Auf die richtige Härte kommt es an!
Im Verbrennungsmotor, in Gleitlagern und in der Raumfahrt: Diamantähnliche Kohlenstoffbeschichtungen (DLC) vermindern Reibung und Verschleiß in Reibkontakten. Meist enthalten die dabei in Lagern und Motoren genutzten Schmierstoffe das Additiv Zink-Dialkyl-Dithiophospat (ZDDP), das seinerseits Stahloberflächen gegen Verschleiß schützt. Unglücklicherweise kann es die DLC-Schicht angreifen, was zum vorzeitigen Ausfall führt. Forscherinnen und Forscher am Fraunhofer IWM haben herausgefunden, wie die antagonistische Wechselwirkung zwischen den beiden Stoffen entsteht. Im Journal Nature Communications erklären sie, warum DLC-Schichten in Verbindung mit ZDDP auch zu hart sein können.
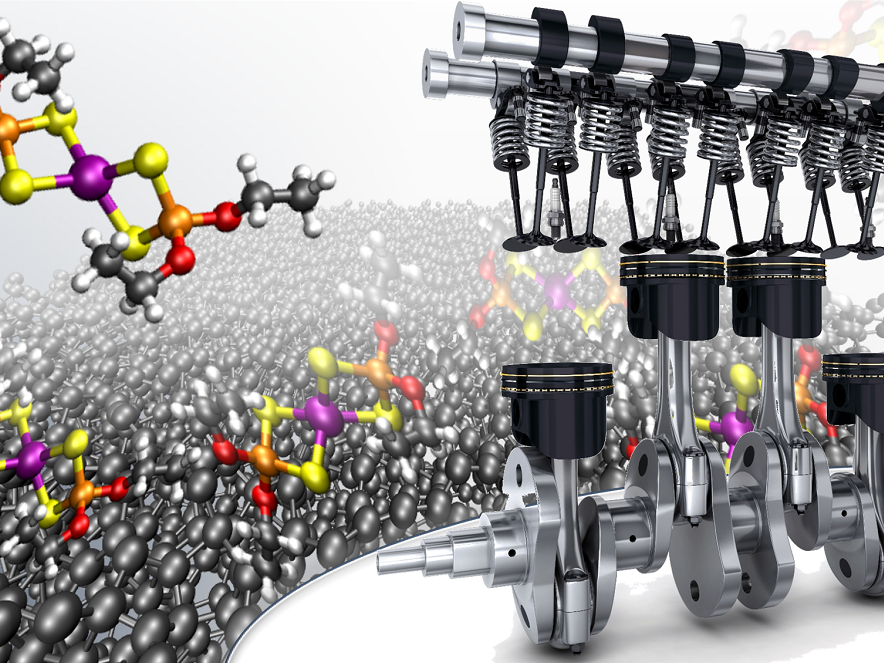
Harte Kohlenstoffbeschichtungen sind weltweit im großindustriellen Maßstab im Einsatz. Aufgrund ihrer guten Oberflächenpassivierung verhindern sie die atomare Anbindung der reibenden Körper aneinander und ihre hohe Härte schützt das darunterliegende Material gegen Verscheiß. Ein besonders starker Nutzer ist die Automobilindustrie, die jährlich mehr als 100 Millionen beschichteter Teile einsetzt mit einem Marktvolumen von mehreren 100 Millionen Euro. Die Schichten sorgen für eine geringere Reibung und somit für geringeren Verbrauch von Antriebsenergie und damit weniger CO2-Ausstoß. Bisher gaben Publikationen zwar Hinweise darauf, dass ZDDP die DLC-Schicht angreifen könnte, es war jedoch unklar, ob dies immer der Fall ist und wie dieser Effekt vermieden werden kann. In dem vom Bundesministerium für Wirtschaft und Energie (BMWi) finanzierten Projekt »Prometheus« hat sich das Fraunhofer-Institut für Werkstoffmechanik IWM mit Firmen aus der Schmierstoffentwicklung und der Automobilindustrie zusammengeschlossen, um unter anderem die tribologischen Prozesse zwischen den DLC-Schichten und Additiven zu entschlüsseln. Dabei arbeitete das Fraunhofer IWM mit der École Centrale de Lyon als externem Partner zusammen.
Experimente mit unterschiedlich harten Schichten
»In den DLC-Schichten verwenden wir tetraedrisch gebundene wasserstofffreie amorphe Kohlenstoffe, ta-Cs«, erklärt Prof. Dr. Michael Moseler, Leiter der Gruppe »Multiskalenmodellierung und Tribosimulation« am Fraunhofer IWM. »Diese gibt es in unterschiedlichen Härtegraden und dementsprechend unterscheiden sich auch andere ihrer mechanischen Eigenschaften.« Deshalb betrachteten die Wissenschaftlerinnen und Wissenschaftler in allen Experimenten und Simulationen nicht nur verschiedene Schmierstoff-Zusammensetzungen, sondern auch verschiedene ta-C-Schichten.
Zunächst musste das Projektteam die Reibungskoeffizienten und den Verschleiß für verschiedene ta-C-Schichten in Verbindung mit unterschiedlich zusammengesetzten Schmierstoffen ermitteln. Dies untersuchte Prof. Dr. Maria-Isabel de Barros Bouchet und ihre Mitarbeitenden am Laboratoire de Tribologie et Dynamique des Systèmes (LTDS) in mehreren Versuchen. »Die Daten werden erhoben, indem man einen Zylinder auf einer Platte entlang einer Strecke von 10 mm hin und her bewegt«, erläutert Prof. Moseler. »Dies untersucht man für die verschieden harten Beschichtungen jeweils mit einem Grundöl und einem ZDDP-haltigen Schmierstoff.« So lässt sich der Verschleiß messen und der Reibungskoeffizient berechnen. Verwendeten die Wissenschaftlerinnen und Wissenschaftler das Grundöl, waren Reibung und Verschleiß wie erwartet umso kleiner, je härter die DLC-Schicht war.
Bei den Versuchen, in denen dem Öl 1 Prozent ZDDP beigemischt wurden, zeigte sich ein überraschenderes Bild: »Bei der vergleichsweise weichen Schicht, dem ta-C(51), bleiben Reibung und Verschleiß gering. Bei den härteren Beschichtungen ta-C(66) und ta-C(78) jedoch gehen Reibung und Verschleiß durch die Decke!«, sagt Dr. Gianpietro Moras – Koautor und Teamleiter in Prof. Moselers Gruppe. Dies sei nicht nur für die Motorenanwendung sehr kritisch, sondern auch aus tribologischer Sicht untypisch. »Normalerweise gehen wir davon aus, dass mit zunehmender Härte der Verschleiß abnimmt«, so der Tribologie-Experte.
Simulationen zeigen: Härter ist nicht immer besser
Die Tribologinnen und Tribologen am Fraunhofer IWM suchten den Grund für dieses Phänomen in Bindungsverhältnissen der Materialien. In einer Röntgenphotoelektronenspektroskopie-Analyse zeigten sie, dass während des Reibens sowohl beim ta-C(66) als auch ta-C(78) viele Schwefel-Kohlenstoffverbindungen entstehen. »Das ZDDP-Molekül enthält viel Schwefel«, sagt Moras. »Unsere Quantenmolekulardynamikrechnungen zeigen, dass das Molekül während des Reibens unter hohen Flächenpressungen dissoziiert und damit der Schwefel freigesetzt wird. Dieser gelangt in die harten Schichten, welche durch diese Dotierung massiv an Festigkeit verlieren und damit anfälliger für Abrieb werden.«
Mit Kontaktmechanik-Rechnungen konnte Moselers Gruppe den Grund für die Schwefel-Dotierung herleiten: »Der lokale Druck, der entsteht, wenn zwei Oberflächen gegeneinanderstoßen, hängt maßgeblich von der Härte und Steifigkeit der Schichten ab«, erklärt Moseler. Konkret bedeute dies: Je steifer die Schicht, desto größer ist die lokale Pressung zwischen den beiden Oberflächen. »Wir modellieren möglichst genau, was an der Grenzfläche zwischen den beiden Reibpartnern passiert. Mit geringer Flächenpressung wird das ZDDP-Molekül zerrieben und bildet eine glasige Schutzschicht zwischen den beiden Reibpartnern.« Dies ist der gewünschte Effekt des Schmierstoffs. »Bei höherer Flächenpressung wird das Molekül auch zerrieben, aber der Druck ist dann so groß, dass die beiden Oberflächen quasi miteinander verbacken und der Schwefel in beide Flächen eingerieben wird.« Diese sogenannte Kaltverschweißung schwäche die DLC-Schicht und führe zu erhöhtem Verschleiß. »Die Industrie kann durchaus ta-C-Schichten verwenden«, schlussfolgert der Tribologe, »Die Schicht darf nur nicht zu weich sein, damit die Reibung nicht zunimmt und nicht zu hart, weil sonst der Verschleiß zunimmt.«
Mit DLC-Schichten fit für die Zukunft
Dieses Wissen ist nicht nur für Verbrennungskraftmaschinen wichtig, so Moseler. »Unser Beispiel war zwar ein Verbrennungsmotor, aber ZDDP wird zum Beispiel auch in Wälzlagern eingesetzt. Daher gibt es viele weitere Anwendungen, wie in Elektroautos, Windkraftanlagen und in der Zukunft vielleicht auch im Wasserstoffmotor.«
Prof. Dr. Moseler und seine Gruppe haben sich bereits vor 15 Jahren darauf spezialisiert, tribologische Systeme auf der atomaren Skala zu verstehen. »Prometheus« ist ein durch das Bundesministerium für Wirtschaft und Energie (BMWi) finanziertes Verbundvorhaben zur Reibungs-Optimierung von Motoren durch Einsatz von triboaktiven Hochleistungskohlenstoff- sowie Eisenbasisschichten und Schmierstoffen; Förderkennzeichen: 03ET1609E.
Salinas Ruiz, V.R.; Kuwahara, T.; Galipaud, J.; Masenelli-Varlot, K.; Ben Hassine, M.; Héau, C.; Stoll, M.; Mayrhofer, L.; Moras, G.; Martin, J.M.; Moseler, M.; de Barros Bouchet, M.-I., Interplay of mechanics and chemistry governs wear of diamond-like carbon coatings interacting with ZDDP-additivated lubricants, Nature Communications 12 (2021) Art. 450, 15 Seiten Link
Publikationsangaben auf Fraunhofer Publica Link