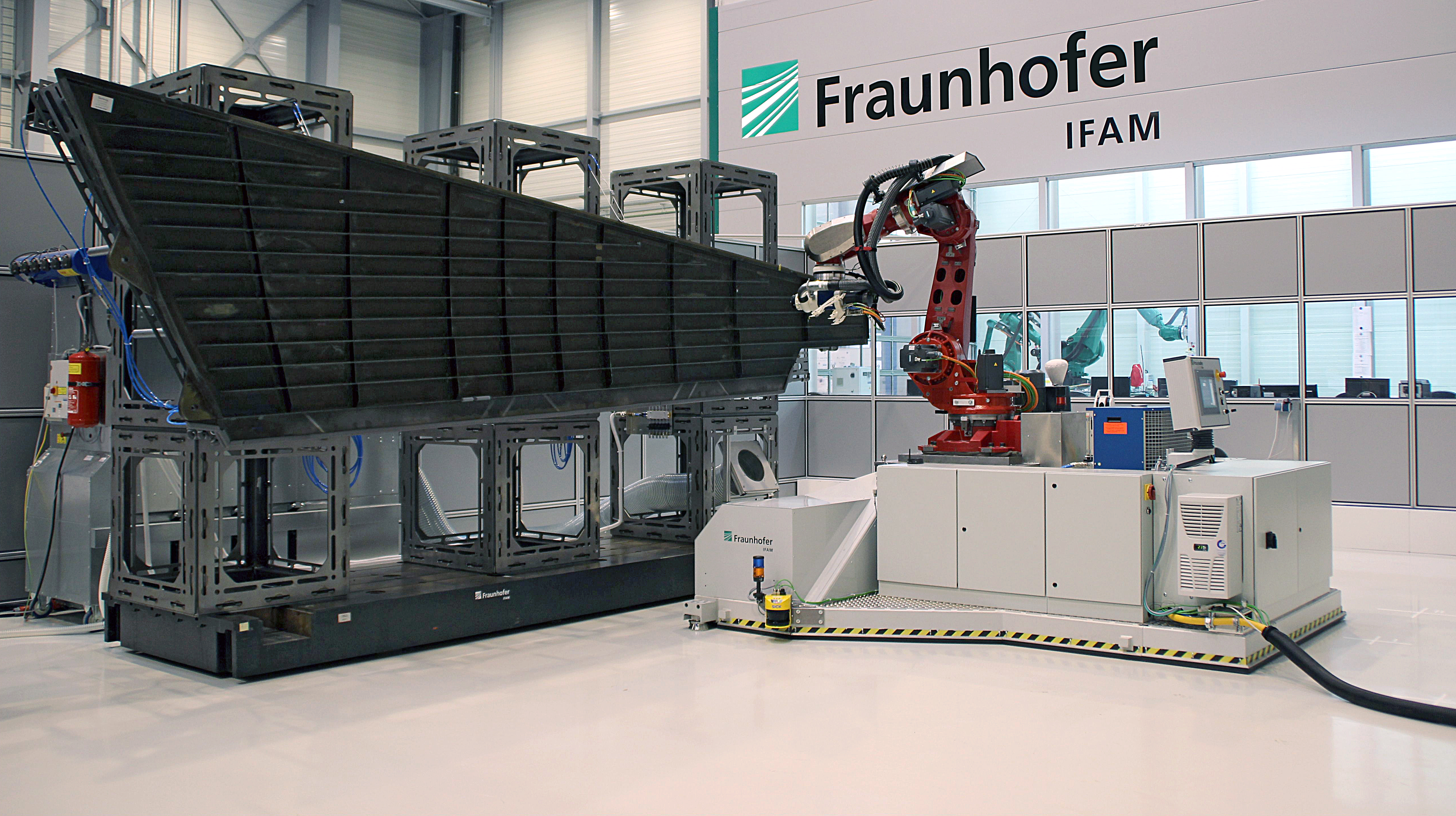
Für große Leichtbaustrukturen, z.B. im Flugzeugbau, werden meist auch große Bauteile aus Leichtbauwerkstoffen wie carbonfaserverstärkte Kunststoffe (CFK) oder Aluminiumlegierungen verwendet. Größe sorgt hier für eine besondere technische Herausforderung. Zum einen weisen die Bauteile herstellungs- und steifigkeitsbedingt relativ hohe, individuell unterschiedliche Abweichungen von der idealen Geometrie auf, zum anderen müssen bei der Bearbeitung und Montage sehr geringe Toleranzen eingehalten werden. Vielfach dürfen Abweichungen vom Designoptimum nur ± 0,2 Millimeter betragen, manchmal sogar noch weniger. Diese Randbedingungen führten das Fraunhofer-Institut für Fertigungstechnik und Angewandte Materialforschung IFAM, Stade, im Projekt ProsihP 2 zu einer außergewöhnlichen Lösung der Aufgabe, bestehende Portalanlagen zum Umrissfräsen großer CFK-Schalen durch eine effizientere und kostengünstigere Technologie auszutauschen, die zudem eine höhere Flexibilität mitbringt.
Das aussichtsreichste Konzept besteht darin, eine Portalanlage durch drei mobile Roboter flächen- und investitionsneutral zu ersetzen. Daraus ergibt sich ein Produktivitätsgewinn von ca. 40 Prozent. Ein zusätzlicher Vorteil der mobilen Roboter ist – auch nach Endeffektorwechsel – der Einsatz andernorts für weitere Aufgaben.
Somit ergab sich für die Projektpartner die Herausforderung, ein System aus autonomem Bodenfahrzeug (AGV) und Industrieroboter zu entwickeln, das Bauteile individuell vermisst und hinreichend genau bearbeitet. Da am Markt weder Roboter mit der benötigten Absolutgenauigkeit noch AGV mit der nötigen Steifigkeit verfügbar waren, entschlossen sie sich, das AGV neu zu konstruieren und einen marktgängigen Roboter motorisch, steuerungstechnisch und sensoriell nachzurüsten.
Das kosteneffizient aus Standardkomponenten aufgebaute AGV ist für austauschbare und herstellerunabhängig wählbare Schwerlastroboter mit bis zu 2,6 Tonnen Gewicht gebaut. Es setzt für die Prozessdurchführung mit drei Stützen statisch bestimmt auf dem Boden auf. Destabilisierende Effekte des Fahrwerks werden so vermieden. Drei ausfahrbare Räder geben dem AGV eine weitreichende Bewegungsfreiheit bis zur Drehung auf der Stelle.
Das Projektteam stattete die Kinematik des Roboters mit einer Siemens CNC-Steuerung aus, baute kompatible Motoren ein und ergänzte abtriebsseitige Winkelmesssysteme an jeder Achse zur Korrektur von Positionsabweichungen. Vor Prozessbeginn wird der Roboter mit einem Verfahren kalibriert, das auf dem Ersatz des kinematischen Robotermodells durch ein individuell parametrisiertes Modell basiert. Zudem ermitteln Kameras oder Lasertracker die aktuelle Pose des Roboters für eine Echtzeitkorrektur durch Abgleich mit den Soll-Daten. Durch die gemeinsame Entwicklung ist nicht nur der einzige mobile Bearbeitungsindustrieroboter entstanden, der die Anforderungen der Luftfahrt erfüllt, sondern der genaueste weltweit.
Das auf der Hannover Messe mit dem ROBOTICS AWARD 2018 ausgezeichnete System ist bisher für Bauteile mit Längen bis zu 30 Metern ausgelegt. Damit ist es für verschiedene Flugzeug-Primärstrukturen wie Flügelschalen oder Rumpfsegmente anwendbar. Zudem kann es mit geringen Modifikationen z.B. für Rotorblätter von Windkraftanlagen oder Großbauteile im Schiffsbau zum Einsatz kommen.
An dem durch das Land Niedersachsen geförderten Projekt waren beteiligt: Aicon 3D Systems GmbH, Airbus Operations GmbH, Artis GmbH, CTC GmbH Stade, Fraunhofer IFAM, IPMT der TU Hamburg, Ludwig Schleicher Anlagenbau GmbH, Mabi AG – Robotic, mz robolab GmbH, Siemens AG und Volkswagen AG.