Von Korngrenzen bis Crashsicherheit: Prozesskettensimulation für die Bauteilentwicklung
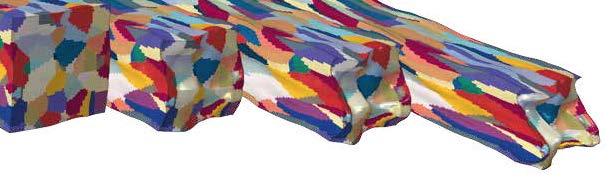
Den Simulationsexpertinnen und -experten am Fraunhofer IWM ist es gelungen Herstellungsprozesse vom Halbzeug bis zum Endprodukt durchgängig zu simulieren – beispielsweise für Blech-, Schmiede-, geschweißte oder pulvertechnologisch hergestellte Bauteile. So besteht die Voraussetzung, mögliche Schwachpunkte im Werkstoff wie Risse oder unerwünschte Eigenschaften sowie deren Fortpflanzung in der Prozesskette zu identifizieren. Dadurch können sie behoben und die Bauteile optimal für ihren Einsatz qualifiziert werden.
Die Tatsache, dass sich die Mikrostruktur eines Werkstoffes während der Bearbeitungsprozesse stark verändert und einen entscheidenden Einfluss auf das Einsatzverhalten des fertigen Bauteils hat, verlangt nach neuen Simulationskonzepten.
Während die numerische Beschreibung einzelner Prozessschritte weitgehend etabliert ist, bietet das Fraunhofer IWM seinen Kunden mehrskalige, nahtlos miteinander verknüpfte Simulationen entlang der gesamten Prozesskette an. Die Integration der Prozessgeschichte, die Struktur und Eigenschaften eines Werkstoffes beeinflusst, ermöglicht den Wissenschaftlerinnen und Wissenschaftlern, das Betriebsverhalten eines Bauteils präzise vorherzusagen. Damit bekommen Kunden das Know-how an die Hand, um Prozessparameter problemspezifisch anzupassen und erhalten kompetente Unterstützung zur Modellentwicklung oder zur Optimierung spezifischer Prozessketten.
Insbesondere in den Branchen der Stahl- und Metallverarbeitung, der Automobilzulieferung, im Fahrzeug- und Anlagenbau und bei der Herstellung von keramischen Bauteilen kann dies zu erheblicher Zeit- und Kosteneinsparung führen, da Produktentwicklungszyklen deutlich reduziert werden. Um den zentralen Anforderungen von Leichtbau, Crashsicherheit und langer Lebensdauer zu genügen, werden die Simulationen entlang der Prozesskette auf mehreren Skalen parallel durch experimentelle Untersuchungen und Validierungen begleitet. Beispielsweise umfasst die Umwandlung eines Millimeter dünnen, metallischen Warmbandes in eine tragende Säule einer Automobilkarosserie aus Dualphasenstahl das Kaltwalzen, die Wärmebehandlung und die Umformung zum fertigen Bauteil. Das am Computer nachgebildete Gefüge des Warmbands dient der Kaltwalzensimulation als Eingangsdatensatz. Diese Finite Elemente-Simulation bildet die Entwicklung der Textur während des Walzprozesses und die damit verknüpften Materialeigenschaften ab. Die Ergebnisse werden in der darauffolgenden Glühsimulation weiter verarbeitet.
Das Team arbeitet zurzeit daran, ausgehend von der Mikrostruktur aus der Glühsimulation die makroskopischen Materialparameter mit dem am Fraunhofer IWM entwickelten »virtuellen Labor« noch detaillierter bestimmen zu können. Virtuelle, makroskopische Spannungs-Dehnungs-Kurven liefern hierbei die Materialparameter für die in der anschließenden
Umformsimulation eingesetzten Modelle. Das Besondere an dem Zwischenschritt des virtuellen Labors ist die Möglichkeit, Versuche in der Simulation abzubilden, die in der Praxis für Blechwerkstoffe nur schwer oder gar nicht realisierbar sind.
Die abschließende Simulation der Ermüdungsfestigkeit oder Crashsicherheit des Bauteils bewertet die Versagensursachen unter Berücksichtigung möglicher Vorbelastungen wie Blechausdünnungen oder lokalen Schädigungen, die aus den vorherigen Prozessschritten stammen.