Erstentwicklung von Prozessparametern für den 3D-Druck von Schwermetallen und Sonderwerkstoffen
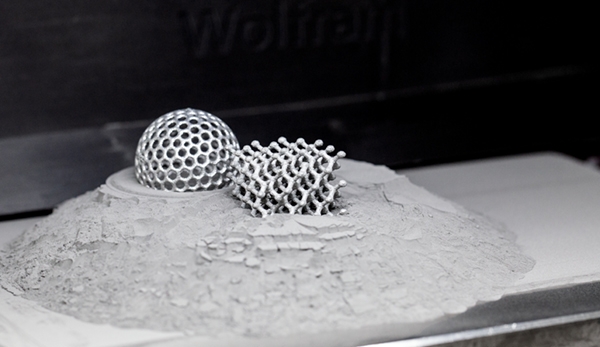
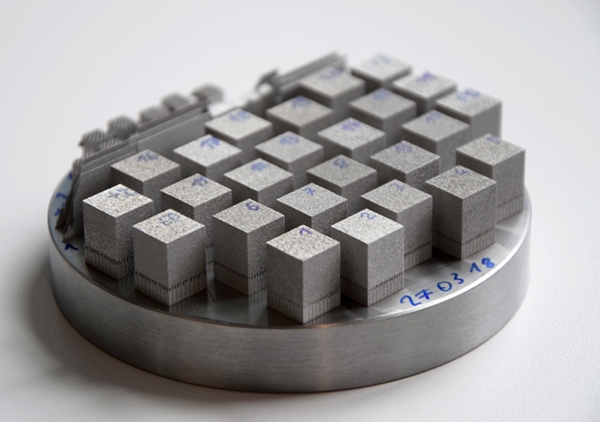
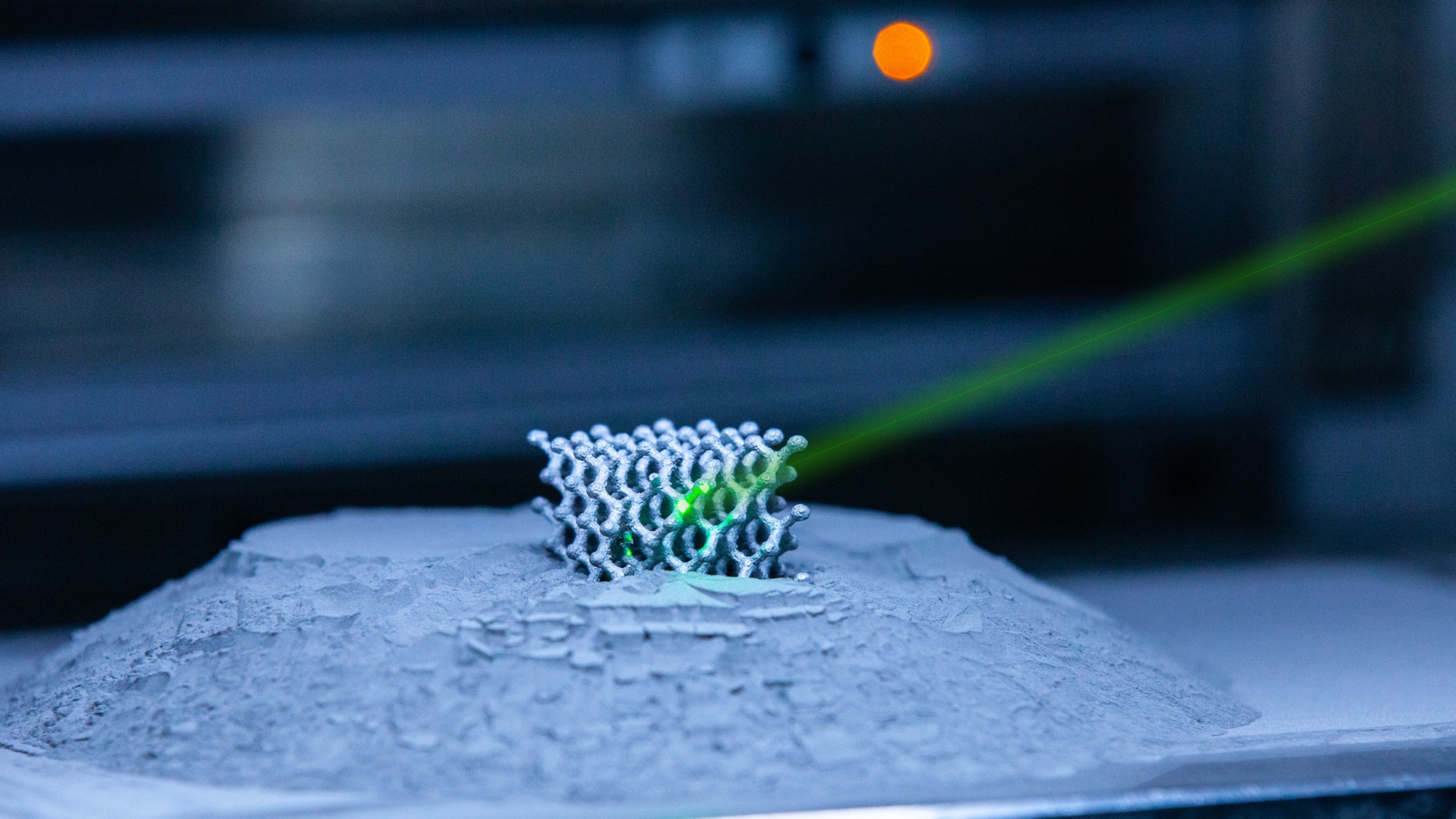
Die additive Fertigung (3D-Druck) hat sich in den letzten Jahren rasant weiterentwickelt und wird zunehmend auch zur Kleinserienfertigung in der Industrie eingesetzt. Aufgrund der verschiedensten Anwendungsfelder wächst das Werkstoffportfolio der vielfältigen 3D-Drucktechnologien stetig. Die besonders ausgeprägte Werkstoffflexibilität des pulverbettbasierten Laserverfahrens LBM (Laser Beam Melting) macht es zum am weitesten verbreiteten metallischen 3D-Druckverfahren. Dünne Schichten von Metallpulver werden bei diesem Verfahren auf ein Substrat aufgetragen, durch Laserenergie lokal aufgeschmolzen und mit der vorherigen Schicht verbunden. Auf diese Weise entsteht aus vielen Schichten ein dreidimensionales Objekt. Durch dieses additive Prinzip ergeben sich neue Freiheitsgrade im Design. Zusätzlich können auch komplexe Formen für Werkstoffe generiert werden, die konventionell zum Beispiel wegen ihrer hohen Härte nur sehr schwer bearbeitet werden können. Weitere Vorteile des LBM sind Flexibilität, die Möglichkeit integraler Bauweisen und Funktionsintegration, verbesserte Logistik, reduzierte Entwicklungszeiten und individuelle Produkte. Grundsätzlich ermöglicht LBM im Vergleich zu konventionellen Verfahren vergleichbare Materialdichte und hervorragende Materialeigenschaften. Die Technologie eignet sich somit sehr gut für die Herstellung hochbelasteter, auf Leichtbau optimierter Maschinenteile oder für Funktionsanwendungen in der Wehrtechnik.
Bislang wenige Legierungen für vielfältige Anwendungsfelder
Aufgrund der momentan aufwendigen Parameterentwicklung neuer Legierungen für den LBM-basierten 3D-Druck kommen vor allem wenige ausgewählte Legierungen für breite Anwendungsfelder zum Einsatz. Aluminium- und Titanlegierungen bedienen den Leichtbaumarkt. Nickelbasislegierungen eignen sich für Hochtemperaturanwendungen, Edelstahl für den Maschinenbau und die Herstellung von Kunstobjekten, Cobaltchrom- und Titanlegierungen decken den Markt der Medizintechnik ab, und hochfeste Stähle werden zur Herstellung von Werkzeugen eingesetzt. Einsatzbereiche mit Bedarf nach alternativen Werkstoffen werden momentan nur bedingt bedient. Speziell für dynamische Anwendung, wie im Bereich Fahrzeugcrash und insbesondere in vielen Bereichen der Wehrtechnik, finden sich kommerziell momentan keine geeigneten Materialien. Das Fraunhofer EMI entwickelt darum eigene Fertigungsparameter für die Verarbeitung von Sonderwerkstoffen. Einen Schwerpunkt bildet hierbei der wehrtechnische Bereich Schutz und Wirkung.
Hochqualitative Schwermetalle aus dem 3D-Drucker
So wurden beispielsweise Parameter zur Herstellung von hochqualitativem Wolfram entwickelt. Das Element zeichnet sich durch seine hohe Dichte und den höchsten Schmelzpunkt aller Metalle aus. Die Verarbeitung von Refraktärmetallen wie Wolfram zeigt hierbei, dass sich im LBM-Verfahren auch konventionell schwierig zu bearbeitende Metalle verarbeiten lassen, obwohl diese generell als schlecht schweißbar gelten und das LBM-Verfahren im Grundprinzip einem Laserschweißprozess ähnelt. Die Parameterentwicklung für Wolfram stellte die Wissenschaftler am EMI vor besondere Herausforderungen. Aufgrund des hohen lokalen Energieertrags und großen Abkühlraten bei der Bearbeitung mit einem Laserstrahl kommt es im Mikrogefüge zu Rissbildungsprozessen. Die Bildung der Mikrorisse konnte im Zuge der Arbeiten erfolgreich minimiert werden. Das Resultat ist ein Sprödwerkstoff mit einer Dichte von etwa 19,2 Gramm pro Kubikzentimeter, ein stark mikrorissreduziertes und dichteoptimiertes Reinwolfram aus dem 3D-Drucker. Der Werkstoff eignet sich beispielsweise für Munitionsanwendungen oder Spezialanwendungen, wie Kollimatoren für Röntgendetektoren. Weitere Anwendungsbereiche sind Elektrotechnik, Medizintechnik sowie Applikationsfelder mit höchsten thermischen Anforderungen.
Effiziente Parameterentwicklung und Optimierung dank hausinterner Methodik
Für die Entwicklung der Parametersätze kommt eine effiziente, hausinterne Methodik zum Einsatz. Diese ermöglicht eine vergleichsweise schnelle und aufwandsarme Entwicklung der Prozessparameter. Auch lassen sich so besonders teure Spezialwerkstoffe deutlich günstiger entwickeln. Die Methodik stützt sich auf die Betrachtung der Interaktion zwischen Laserstrahl und Metallpulver sowie auf statistische Versuchspläne. Die gewonnenen Erkenntnisse dienen später auch der anwendungsspezifischen Parameteroptimierung sowie der Parameteranpassung für spezifische Bauteile und deren Anforderungen an die Fertigung. Für erste Charakterisierungen der resultierenden Materialien kommen schnelle Verfahren, wie die Bestimmung der Dichte, zum Einsatz. Ist der Parametersatz ausgereift, wird das Material mithilfe modernster Messmittel, wie Elektronenrückstreubeugung (EBSD) oder Mikro-CT-Aufnahmen, charakterisiert, und die Parameter werden weiter verfeinert.
Die Entwicklung einer hausinternen Methodik zur Parameterentwicklung für LBM-Werkstoffe ermöglicht eine effiziente Generierung von Fertigungsparametern und somit den Einsatz optimaler Werkstoffe für spezifische Anwendungsfelder. Es wurde gezeigt, dass sich so auch schwierig zu verarbeitende Werkstoffe in hoher Qualität erzeugen lassen. Denkbar ist in Zukunft zudem die Entwicklung neuartiger Legierungen, welche sich konventionell nicht realisieren lassen. So könnte die hohe Abkühlrate des Prozesses beispielsweise eine höhere Löslichkeit von Legierungselementen und somit neue Werkstoffeigenschaften ermöglichen. Bei der Auswahl zukünftiger Legierungen ist jedoch nicht nur das Anwendungsgebiet zu berücksichtigen, sondern auch der erweiterte Lösungsraum bezüglich der neu verfügbaren Designfreiheiten. Werden Anforderungen beispielweise konventionell durch Geometrien basierend auf Halbwerkzeugen gelöst (zum Beispiel auf Platten), so werden diese bei der Anwendung additiver Verfahren eventuell effizienter durch alternative Geometrien (zum Beispiel durch Gitterelemente) gelöst. Basierend auf der neuen Geometrie gilt es, einen passenden Werkstoff auszuwählen.