Metallische Implantatwerkstoffe – Hochporös und degradierbar
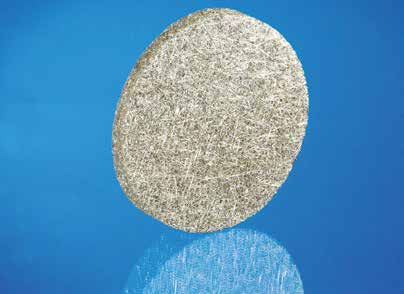
A problem that still hasn’t completely been resolved in the field of medicine is the treatment of large bone defects. These types of lesions do not heal spontaneously and have to be treated with implants. Using the patient´s own bone is the first method of choice for extended bone augmentation, however, the available amount is limited and its removal from the iliac crest poses additional risks. On the other hand, frequent operations that are necessary for removing a synthetic bone replacement create risks in addition to a permanent disruption of the imaging. Degradable materials, i.e. implants that disappear after healing, are considered an ideal solution.
Magnesium Fiber Structures as Materials that are Adaptive to Bones
Magnesium is an almost ideal material. It degrades in a biological environment, has excellent biocompatibility and contains particularly bone-adhering properties.
A magnesium implant has now been developed at Fraunhofer IFAM in Dresden that has favorable characteristics due to its structure. Metallic fiber structures form a highly porous framework that serves as a growth guiding structure for the bone, thus enabling the ingrowth of the blood vessels. Such structures are particularly interesting because of their reduced stiffness; they are very similar to the biomechanical properties of bones. This has a particularly stimulating effect on bone growth.
The starting point for the technological development is the manufacture of short magnesium fibers by extraction from the melt. These fibers are laid down homogeneously and sintered. A particular challenge in the manufacture of magnesium fiber structures is the sintering, which, as a result of the stabile surface oxides, is resistant to the high oxygen affinity of the material. The heat treatment is therefore carried out with a partial melting phase in which precise knowledge of the correct melting point for the sinter result is essential. The appropriate sinter regimes are calculated by simulative methods.
The implants manufactured with this method have good mechanical properties and, above all, very good corrosion properties. As the result of increased separations of Y203 on the grain boundaries, a degradation behavior with reduced corrosion rates could be attained that in particular meets physiological requirements. In animal experiments, a slow rate of corrosion could initially be determined after 12 weeks and a large part of the metallic implant disappeared after 24 weeks.
As a winner of the Innovation Competition in Medical Technology, this approach was funded by the German Federal Ministry of Education and Research (BMBF). In the meantime, these favorable characteristics have convinced enterprises as well. Botiss Dental GmbH has become a licensee for the patent that has, in the meantime, already been granted. The company is planning to implement the material in oral surgery and is presently evaluating the development of a suitable production chain.