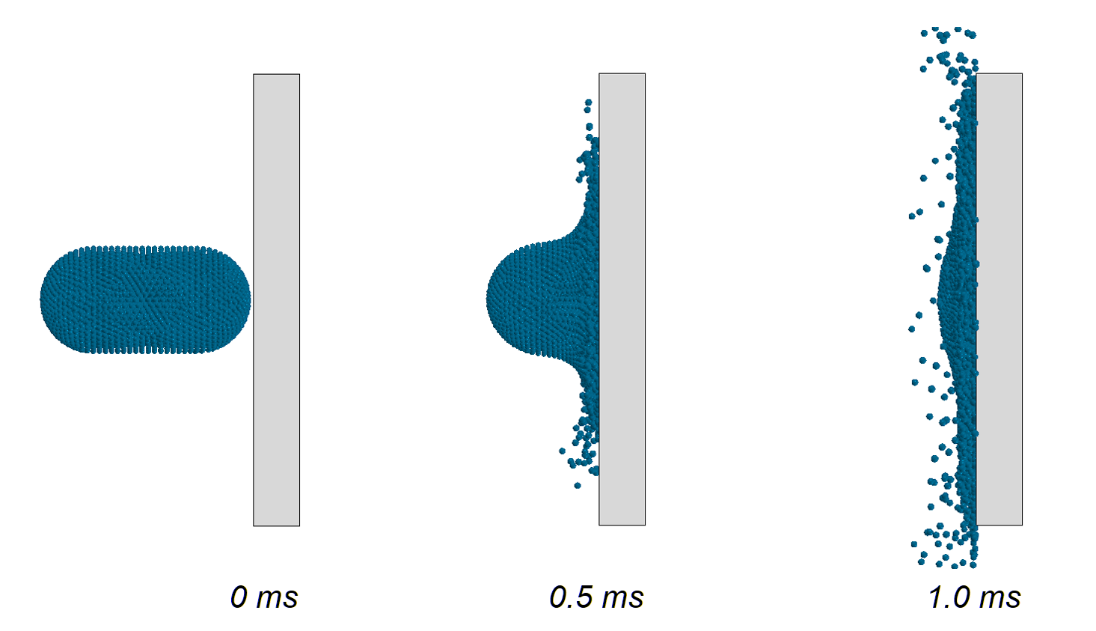
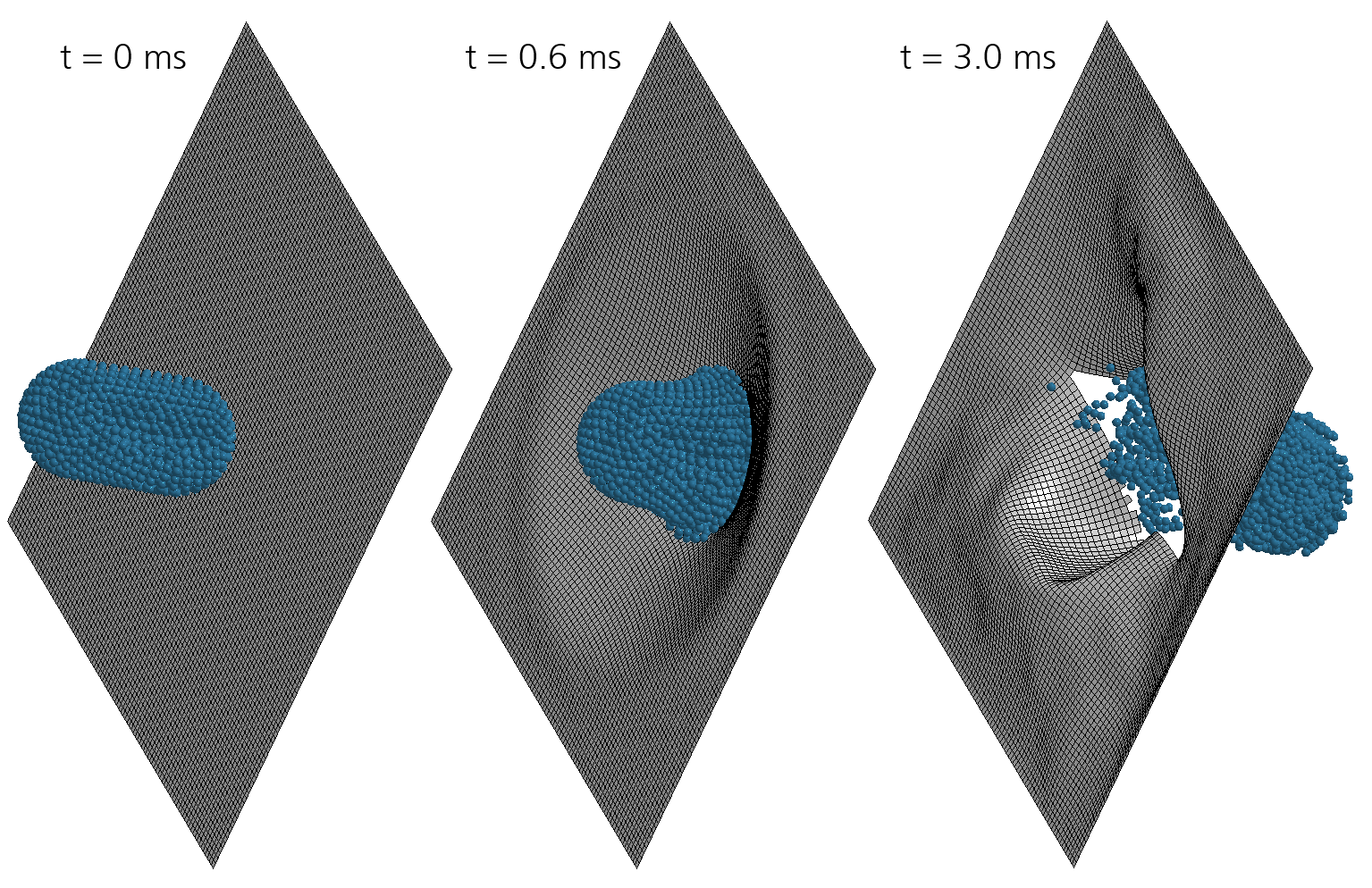
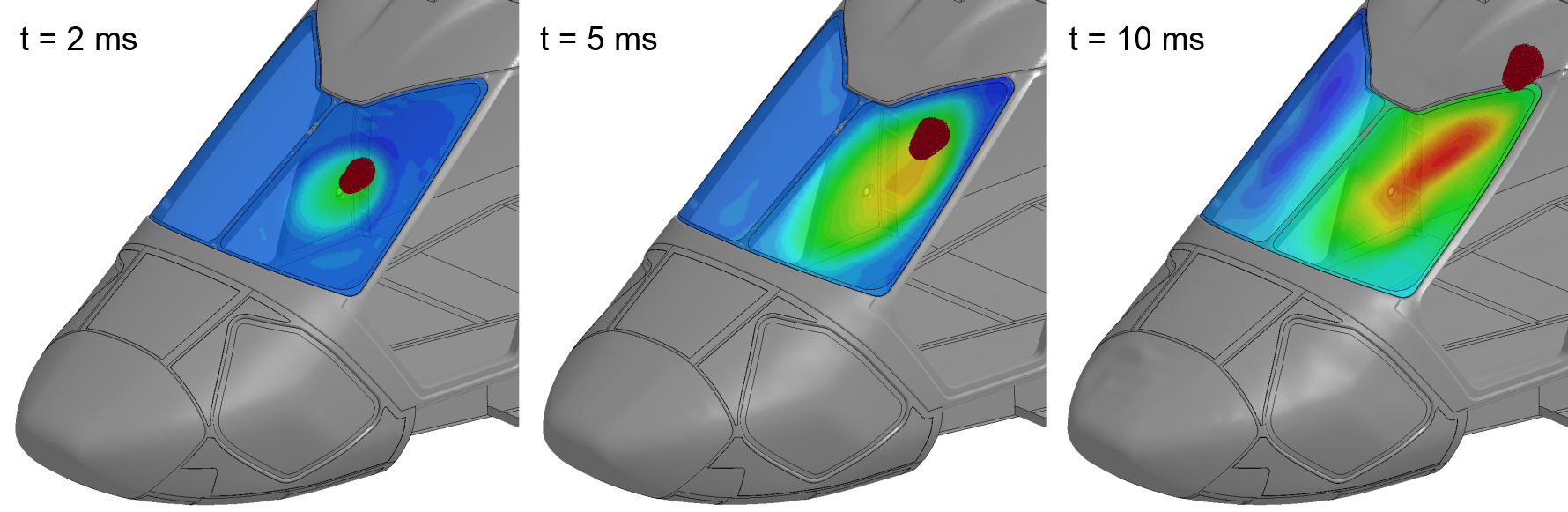
At the Paris Airshow, Airbus Helicopters presented a model of its new high-speed helicopter “Racer” on June 17, 2017 (Figure 1). The Racer demonstrator is being developed within the EU aviation program Clean Sky 2 and is scheduled for its first flight in 2020. Racer, which is short for Rapid And Cost-Effective Rotorcraft, will incorporate several innovative features for attaining a very wide cruising radius and a high cruising speed of over 400 kilometers per hour at very low fuel consumption. This new type of high-speed helicopter is supposed to be deployed for search and rescue missions, emergency medical services as well as public and private supply and transportation flights.
Fraunhofer EMI provides basis for flight permit
For Racer’s first flight in 2020, a flight permit is required, for which Racer has to meet the demands according to EASA standard CS-29. Inter alia, you have to ensure the safe progression of the flight or safe landing after collision with a bird of mass 1 kilogram. Statistical data substantiate the necessity of this: Every year, several 10,000 collisions of birds with aircraft occur world-wide. They cause high economic losses and can sometimes even lead to safety risks, as the New York incident in 2009 shows, when an A320 had to carry out an emergency landing on the Hudson River. Because of the lower flight level, helicopters are more often affected by bird strikes than airplanes. Fraunhofer EMI conducted the simulations necessary to provide this evidence. Airbus Helicopters provided the relevant data, and from these, a finite-element model (FEM) of Racer was generated. Using this model, it is possible to simulate bird strikes at various locations of the helicopter and estimate their effects.
Creating the numerical model
For realistic simulations of bird-strike impact, a validated model of a bird had to be created. This happened in a simplified manner as the exact numerical reproduction of the animal would have been a quite considerable effort. Details of the bird body only play a minor role for damages caused by impact, anyway. That is why birds are usually modeled as simple geometrical forms such as spheres or ellipsoids. Simulation at EMI resorted to the common form of a cylinder with semispherical ends. The bird model was discretized by the SPH method (smoothed particle hydrodynamics). Given the high deformations occurring at impact, this method shows many advantages over classical FE methods with regard to stability and computing time. When subjected to high velocities relevant during a bird-strike event, the material strengths are exceeded by far implying that the material can be modeled by assuming a simple fluid such as water.
To validate the generated model, in a first step, open-access data published by the Air Force Materials Laboratory during the 1970s were used. Experiments in those times included real chickens as well as surrogate bodies made of gelatin impacting on a steel plate where the occurring pressures were measured. In a second step, Airbus Helicopters supplied EMI with recent measurements. In this case, gelatin birds were shot against polycarbonate plates. Both types of experiment were emulated in simulation (Figure 2: top: steel plate; bottom: polycarbonate plate) using the bird model. The computed pressures, forces and damages show high agreement with the experimental data.
Next, the FE model of the helicopter was prepared. For this sake, geometric data were cleaned up, simplified and connected. Then, the materials involved were modeled and the layer structure of the composite materials, the contacts and the boundary conditions were defined. In its final version, the FE model of Racer consists of more than half a million shell and hexahedron elements with edge lengths of about 10 millimeters to 15 millimeters. In spite of this high number of elements, the simulation of one bird strike takes only a computing time of about one to two hours on 16 central processing units.
Evaluation of bird-strike resistance
The generated model made virtual bird-strike analyses for the high-speed helicopter Racer possible. Figure 3 shows, for example, the deformation of a polycarbonate windshield at collision and subsequent sliding-off of a bird with a relative velocity of about 460 kilometers per hour. Despite strong deformation, the shield stays intact.
The great advantage of using simulations is that it is easily possible to carry out adjustments on the computer concerning materials, wall thickness of components or change of collision point and velocity of the bird. Thus, various scenarios could be analyzed with regard to bird-strike resistance. Evaluation criteria included, for example, the potential perforation or breaking of components, the number of damaged layers of composites, the potential failure of adhesive layers or the residual velocity and the deviation of the bird toward critical structures. These analyses are essential for the preliminary design of the new helicopter. Fraunhofer EMI could identify vulnerable components and make suggestions for improvements. Thus, the work done by EMI is a valuable contribution to the development process of Racer and serves Airbus Helicopters to prove Racer fulfills the requirements for the flight permit.
For further information, visit www.airbus.com