From Grain Boundary to Crash Safety: Process Chain Simulation for Component Development
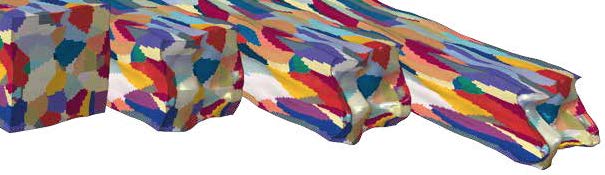
Simulation experts at Fraunhofer IWM have been able to simulate continuous manufacturing processes from semi-finished material to the end product, for example for components manufactured with sheet metal, forging, welded or powder technology. The prerequisite is to identify possible weak points in the material such as cracks or undesirable properties as well as their propagation in the process chain. These can then be removed and the components can be optimally qualified for their application.
The fact that the microstructure of a material changes strongly during the treatment process, and has a decisive influence on the application behavior of the finished component, calls for new simulation concepts.
While the numerical description of individual process steps is established for the most part, Fraunhofer IWM offers its customers multi-scale simulations that are seamlessly linked with each other along the entire process chain. The integration of the process history, the structure and properties of a material all have an impact and enable scientists to precisely predict the operational behavior of a component. This gives customers the knowhow for adapting process parameters to a given situation, and gives them competent support for model development or for the optimization of specific process chains.
Particularly in the steel and metal-working industries, automobile supply, automotive and plant engineering and in the manufacture of ceramic components, this can lead to considerable savings in cost and time, since product development cycles are reduced considerably. In order to meet the central requirements of lightweight construction, crash safety and longer life spans, simulations along the process chain are accompanied in parallel by experimental tests and validations on several scales. For example, the conversion of hot rolled steel strip into a supporting pillar of an automobile body made of dual phase steel entails cold rolls, heat treatment and deep drawing into the finished component. The structure of the hot rolled steel strip that is recreated on the computer serves as an input data set for the cold roll simulation. This finite element solution illustrates the development of the structure during the rolling process and the related material properties. The results are processed in the annealing simulations that follow.
On the basis of the microstructure from the annealing simulation, the team is currently working on more closely determining the macroscopic material parameters with the “virtual laboratory” developed by Fraunhofer IWM. Virtual, macroscopic stress-strain curves supply the material parameters for the models used in the ensuing reshaping simulations. The special feature of the intermediate step with the virtual laboratory is the possibility of reproducing tests in the simulation, which, in practice, is difficult or not feasible at all with sheet materials.
The final simulation of the fatigue strength or crash safety of the component evaluates the causes of failure while taking into account any possible pre-existing loads such as sheet thinning or local damage stemming from previous process steps.