Making Coal Power Plants More Flexible and Durable
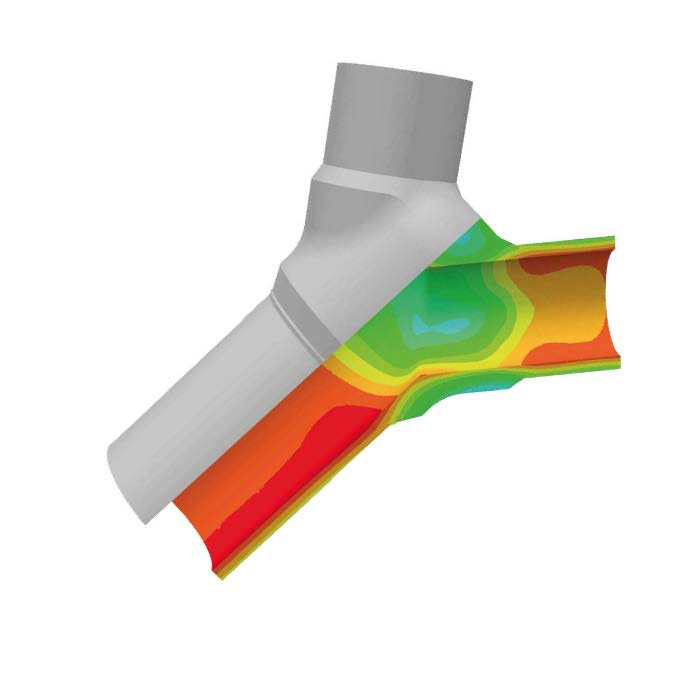
Existing coal power plants must be operated more flexibly in the future. A central question here is what influence the flexible operation mode has on the remaining service life of the power plant components. In the past, these have almost exclusively been designed against creep rupture with TRD or EN standards. Now it is possible to make more precise service life predictions using a new method developed by Fraunhofer IWM taking into account the complex interaction between creep arising from steady state operation and fatigue due to thermal transients generated by flexible operation. Power plant operators will be able to save money, optimize their operations and make their facilities fit for the future using Retro-Fit.
In order to balance out electricity fluctuations coming from regenerative energy sources, conventional power plants will increasingly have to be started up and shut down more quickly in the future. Long-term research and reliable computation methods, however, have not existed up to now for these new demands on components and materials. Fraunhofer IWM is investigating the creepfatigue interaction of high-temperature components.
In contrast to conventional, conservative standards, the resulting lifecycle prediction is much more precise. Power plant operators can avoid the early and expensive replacement of components and can make more solid business decisions on modes of operation.
New materials hold the promise of extending the lifetime of steam cycle components. According to experiments and results of the advanced simulation methods, components made of the nickel-based Alloy 617B last up to six times longer than the same components made of traditional
(ferritic-martensitic) power plant steels. In addition, the power plant may be operated more flexibly by lining the component with thinner walls. A longer lifetime and the reduced amount of material make up for the higher per ton price of the alloy.